Enhancing Operational Efficiency at Barry-Wehmiller: A Fresh Approach to Better Performance
In the manufacturing industry, adopting a pick-and-choose approach when it comes to continuous improvement can sometimes be like hitting up Costco's free sample station - taking a little bit of this or that without fully committing. While this approach might deliver decent results, there's a risk involved: you never quite get the full package and enjoy the savings that come with it.
This approach leads to some concerning long-term issues that can threaten a company's stability and viability. Let's delve into a few of these challenges:
Operational Chaos and Standstill
When processes remain fragmented and disconnected, the result is inconsistent workflows and missed opportunities for end-to-end optimization. The adoption of isolated lean tools can lead to such a scenario, as seen in organizations that don't integrate these tools into a comprehensive framework. Furthermore, when company culture becomes entrenched in risk-averse behavior, employees may revert to obsolete practices when the leadership's improvement efforts fail to align with strategic goals.
Compliance and Quality Issues
A piecemeal approach to improvement can also create vulnerabilities in terms of compliance and product quality. For instance, if a company only partially addresses the cGMP requirements, they leave themselves exposed to potential regulatory action. Additionally, focusing on isolated quality control measures can overlook larger, systemic issues that put the company at risk. It's crucial for streamlined, proactive, and system-wide risk identification to prevent these kinds of oversights.
Financial and Legal Consequences
Ultimately, the failure to properly address these risks can lead to costly remediation efforts in the form of product recalls, litigation, or state enforcement action (such as license revocation). Furthermore, competitors that adopt an integrated lean approach will reap the benefits of faster cycle times and higher profit margins, leaving piecemeal adopters struggling with short-term fixes.
Demotivated Workforce
As employees grow skeptical of disjointed initiatives that fail to deliver tangible benefits, trust in leadership is eroded. This skepticism can eventually lead to talent retention issues, as workers look for organizations with clearer growth pathways and a stronger commitment to innovation.
In order to circumvent these risks and ensure long-term growth, it's essential for a company to adopt a holistic, aligned strategy. This strategy should encompass structured assessments, digital risk management tools, and effective collaboration with vendors. By taking a comprehensive, integrated approach to continuous improvement, manufacturers can ensure their company's stability, optimize their operations, and maintain a motivated and engaged workforce.
- A continuous improvement approach that is fragmented and lacks integration into the overall business strategy may lead to operational chaos, causing inconsistent workflows and missed opportunities for optimization.
- Adopting isolated improvement tools without a comprehensive framework can create vulnerabilities, such as compliance and quality issues, particularly in terms of cGMP requirements.
- A piecemeal approach to improvement can result in costly financial and legal consequences, including product recalls, litigation, and state enforcement action.
- Failing to deliver tangible benefits through disjointed initiatives can lead to a demotivated workforce, potentially causing talent retention issues as employees seek out organizations with a stronger commitment to innovation and growth.
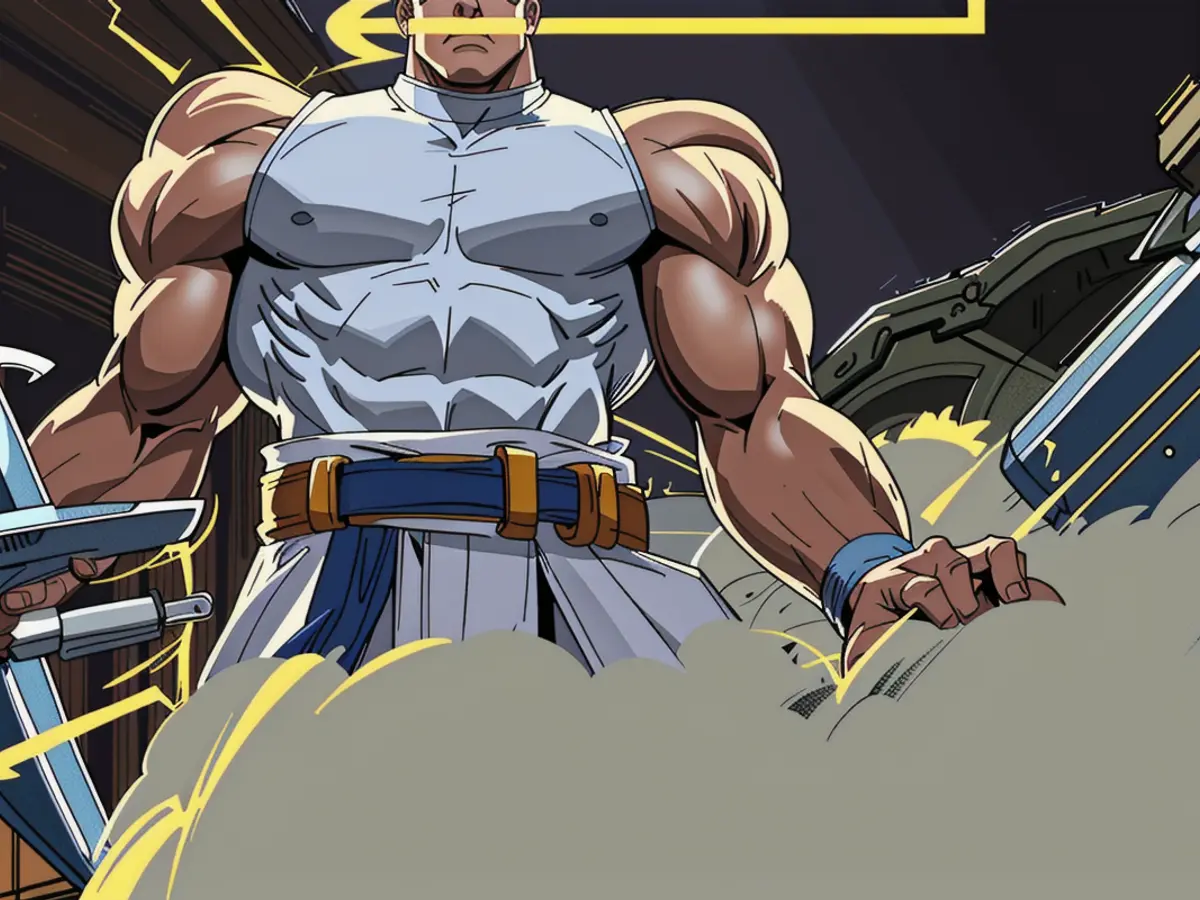
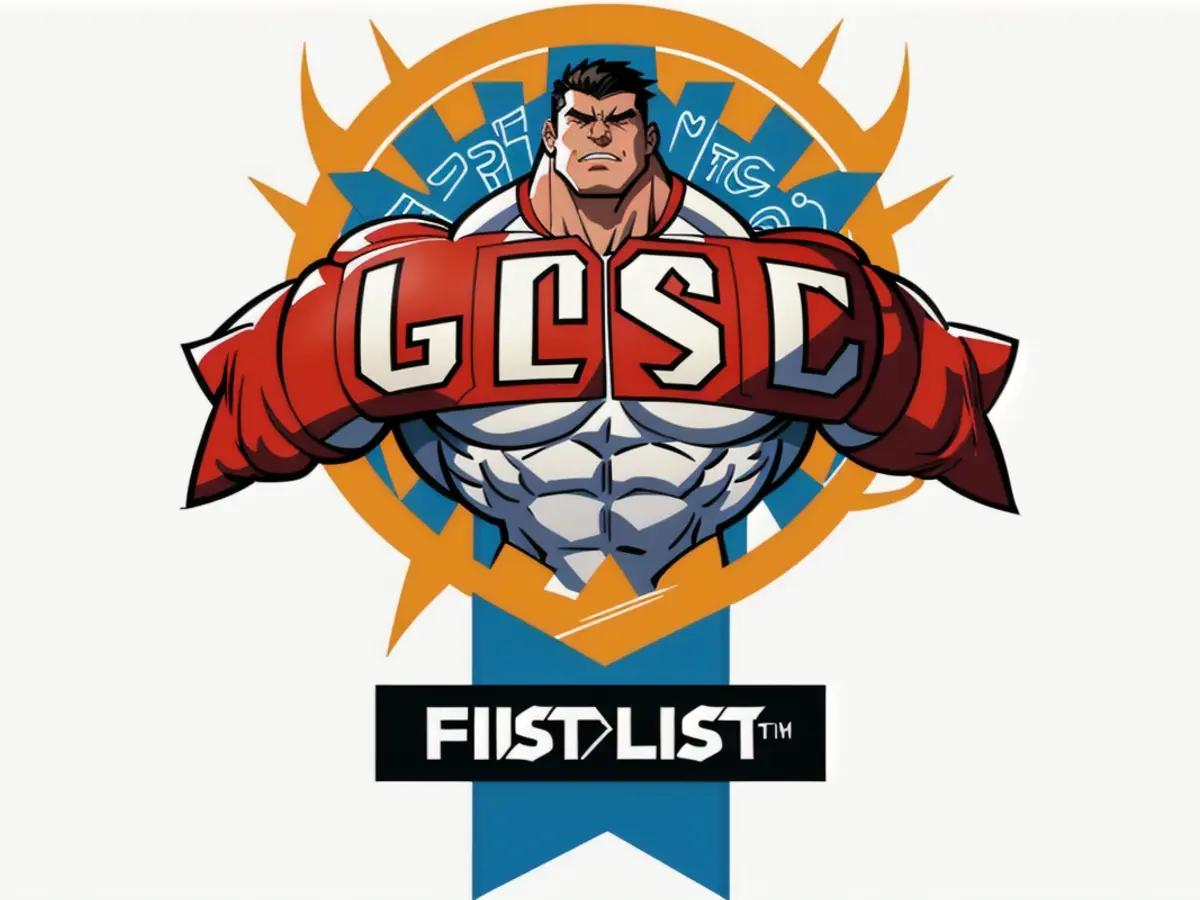
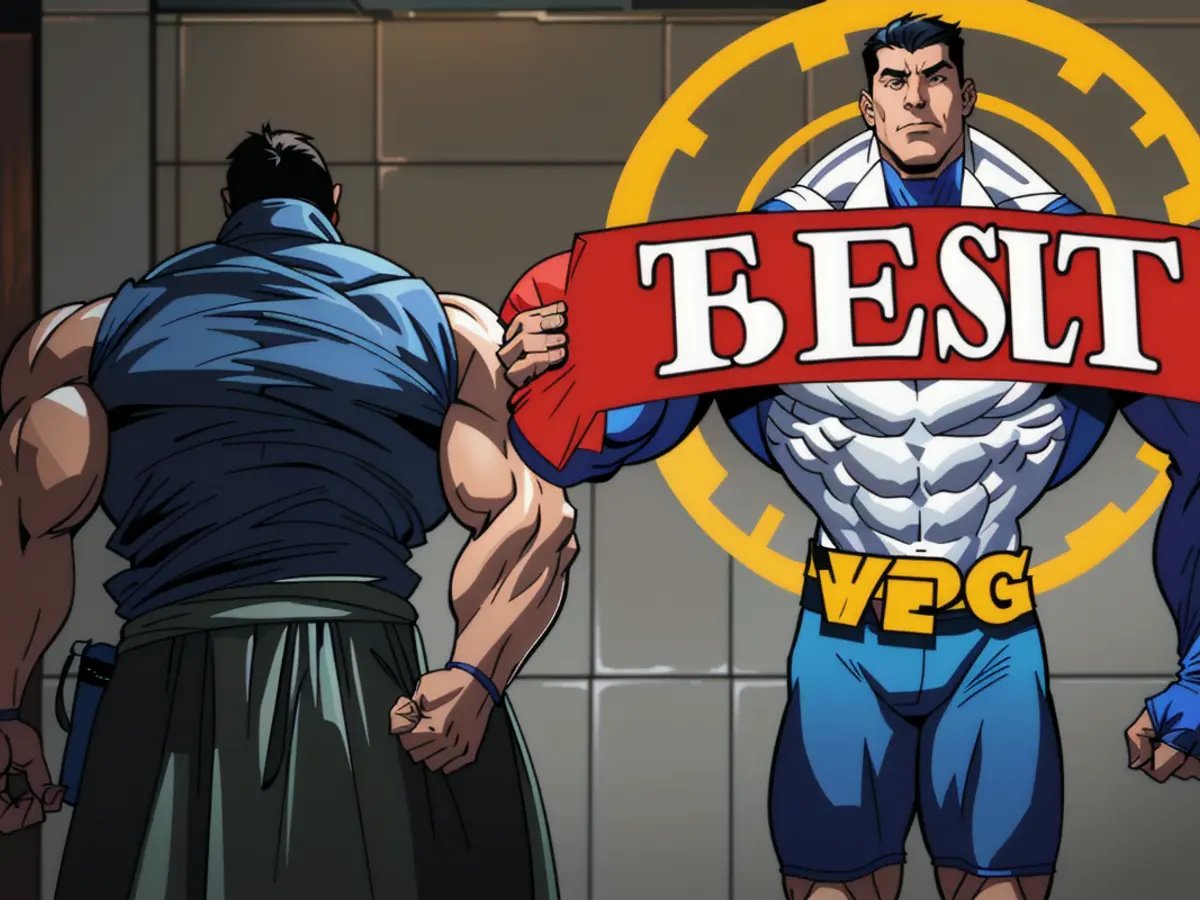